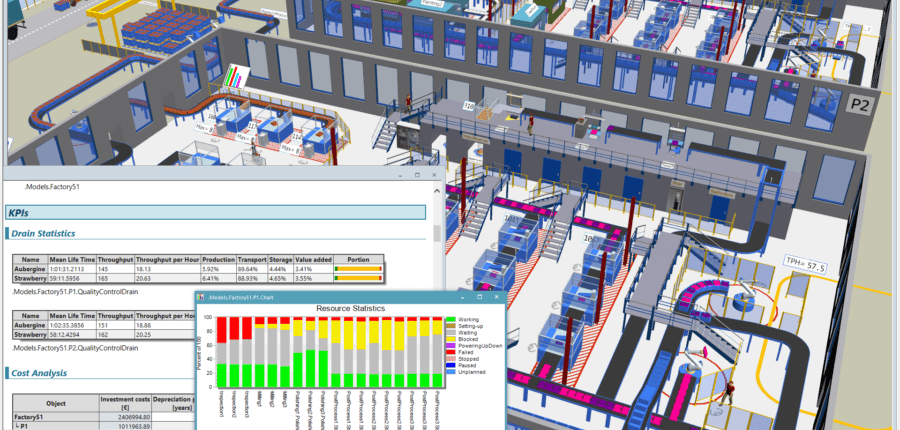
6 Thách Thức trong Tối Ưu Hóa Sản Xuất: Xác Định và Khắc Phục Điểm Nghẽn với Tecnomatix Plant Simulation
Trong môi trường sản xuất ngày nay, các công ty không ngừng nỗ lực tối ưu hóa quy trình để cải thiện hiệu quả và giảm chi phí vận hành. Tuy nhiên, làm thế nào để xác định điểm nghẽn trong hệ thống sản xuất phức tạp? Các điểm nghẽn này không chỉ làm giảm hiệu suất mà còn làm tăng chi phí hoạt động, gây ảnh hưởng đến năng suất tổng thể và khả năng cạnh tranh của doanh nghiệp.
Nhưng làm sao các doanh nghiệp có thể nhận diện chính xác điểm nghẽn và áp dụng các phương pháp khắc phục phù hợp? Điều này đòi hỏi không chỉ công cụ mạnh mẽ mà còn phải có chiến lược phân tích chính xác.
Câu hỏi đặt ra là:
- Làm thế nào để phát hiện chính xác các điểm nghẽn trong hệ thống sản xuất phức tạp?
- Những phương pháp nào trong Tecnomatix Plant Simulation giúp cải thiện năng suất thông qua việc loại bỏ các điểm nghẽn?
- Các doanh nghiệp nên áp dụng những kỹ thuật nào để xử lý điểm nghẽn và tăng hiệu quả hệ thống?
Tecnomatix Plant Simulation của Siemens là một trong những giải pháp hàng đầu, hỗ trợ doanh nghiệp trong việc mô phỏng và tối ưu hóa các quy trình sản xuất. Plant Simulation giúp nhận diện các điểm nghẽn trong hệ thống và cho phép các chuyên gia thử nghiệm nhiều phương pháp để giải quyết các vấn đề này trước khi áp dụng vào thực tế.
Phương Pháp Xác Định Điểm Nghẽn Trong Plant Simulation
Trong Plant Simulation, có nhiều phương pháp xác định điểm nghẽn giúp doanh nghiệp hiểu rõ hơn về những gì đang hạn chế hiệu suất của hệ thống. Dưới đây là các phương pháp chính:
- Xác định điểm nghẽn qua máy sau bộ đệm có lượng công việc trung bình cao nhất
Trong Plant Simulation, một bộ đệm (buffer) với lượng công việc trung bình (Work-in-Progress – WIP) cao có thể là dấu hiệu cho thấy dòng chảy bị tắc nghẽn ở máy tiếp theo. Công cụ Plant Simulation sẽ giám sát lượng WIP tại các bộ đệm trong suốt quá trình mô phỏng. Khi một bộ đệm có lượng WIP trung bình cao, điều này thường chỉ ra rằng thiết bị ở giai đoạn sau đó không xử lý nhanh được lượng công việc đang tồn đọng, và trở thành điểm nghẽn.Ví dụ thực tiễn: Trong một nhà máy sản xuất linh kiện điện tử, bộ đệm đặt giữa giai đoạn lắp ráp và kiểm tra có WIP cao, chứng tỏ máy kiểm tra không đủ công suất để theo kịp tốc độ lắp ráp. Để giải quyết, doanh nghiệp có thể cần nâng cấp công suất của máy kiểm tra hoặc phân chia công đoạn kiểm tra để đảm bảo quy trình không bị gián đoạn.
- Xác định điểm nghẽn qua máy có thời gian sử dụng cao nhất hoặc thời gian chờ ít nhất
Máy nào có tỷ lệ sử dụng cao nhất hoặc thời gian chờ ít nhất thường là điểm nghẽn của hệ thống. Trong Plant Simulation, việc theo dõi thời gian sử dụng của các thiết bị là phương pháp hữu hiệu để xác định giai đoạn nào đang bị quá tải. Khi một máy luôn trong trạng thái hoạt động và có rất ít thời gian nhàn rỗi, điều này chỉ ra rằng máy này không thể đáp ứng đủ yêu cầu, gây ra sự chậm trễ và gián đoạn trong quy trình sản xuất.Ví dụ thực tiễn: Trong ngành công nghiệp ô tô, nếu một máy hàn luôn hoạt động mà không có thời gian chờ, đây là dấu hiệu của một điểm nghẽn. Doanh nghiệp có thể phải đầu tư thêm một máy hàn bổ sung hoặc nâng cao năng suất của máy hiện tại để đảm bảo quy trình không bị tắc nghẽn.
- Xác định điểm nghẽn qua máy sau trạm có tỷ lệ chặn cao nhất
Tỷ lệ chặn cao (high blocking rate) thường cho thấy thiết bị ở giai đoạn tiếp theo không đủ năng suất để tiếp nhận sản phẩm từ trạm trước đó. Plant Simulation có thể đo lường tỷ lệ chặn ở từng trạm để xác định giai đoạn nào trong dây chuyền đang gặp vấn đề. Khi tỷ lệ chặn cao, máy sau trạm này có khả năng là điểm nghẽn, cần được nâng cấp hoặc thay đổi.Ví dụ thực tiễn: Trong chuỗi cung ứng logistics, nếu tỷ lệ chặn cao xảy ra tại trạm đóng gói trước khi đưa hàng vào kho, máy vận chuyển hàng vào kho có thể là điểm nghẽn. Giải pháp là tăng tốc độ vận chuyển hoặc bổ sung máy vận chuyển để tránh tích tụ sản phẩm tại trạm đóng gói.
- Xác định điểm nghẽn qua máy có thời gian hoạt động trung bình dài nhất
Các máy có thời gian xử lý công việc lâu hơn thường tạo ra điểm nghẽn, đặc biệt trong các quy trình có tính đồng bộ cao. Plant Simulation cung cấp chức năng đo lường thời gian xử lý trung bình của từng thiết bị, giúp chuyên gia phát hiện ra các thiết bị nào đang tiêu tốn quá nhiều thời gian trong chuỗi cung ứng.Ví dụ thực tiễn: Trong ngành sản xuất hàng tiêu dùng, máy trộn nguyên liệu có thời gian hoạt động lâu hơn so với các thiết bị khác trong dây chuyền đóng gói. Đây có thể là điểm nghẽn, và doanh nghiệp có thể phải điều chỉnh tốc độ hoặc thêm máy trộn bổ sung để tăng hiệu suất.
- Xác định điểm nghẽn qua máy có độ biến động thấp nhất trong thời gian giữa các lần hoàn thành
Trong Plant Simulation, độ biến động giữa các lần hoàn thành công việc (inter-departure time) là yếu tố quan trọng giúp xác định điểm nghẽn. Các máy có độ biến động thấp nhất trong thời gian này thường tạo ra tốc độ xử lý đều đặn nhưng chậm, có thể gây ra điểm nghẽn nếu các thiết bị khác hoạt động với tốc độ cao hơn. - Xác định điểm nghẽn qua máy nhạy cảm nhất với lưu lượng của hệ thống
Trong một số trường hợp, các máy có độ nhạy cao với tốc độ lưu lượng tổng thể của hệ thống là các điểm nghẽn. Plant Simulation giúp phân tích mức độ nhạy cảm này bằng cách thay đổi lưu lượng hệ thống và đo lường phản ứng của các máy. Máy nào có độ nhạy cao với thay đổi lưu lượng có khả năng trở thành điểm nghẽn khi có sự gia tăng đột ngột về lưu lượng hoặc nhu cầu.
Phương Pháp Khắc Phục Điểm Nghẽn Trong Plant Simulation
Sau khi xác định điểm nghẽn, Plant Simulation cung cấp các phương pháp khắc phục hữu hiệu, giúp giảm thiểu gián đoạn và cải thiện năng suất hệ thống:
- Tăng Số Lượng Máy ở Giai Đoạn Điểm Nghẽn Đối với những máy ở giai đoạn điểm nghẽn có công suất hoạt động quá cao, doanh nghiệp có thể tăng số lượng máy ở công đoạn này để phân chia công việc và giảm bớt áp lực.
Ví dụ thực tiễn: Trong một dây chuyền sản xuất linh kiện điện tử, khi máy lắp ráp là điểm nghẽn, thêm một máy lắp ráp bổ sung có thể giúp giảm thời gian chờ và tối ưu hóa dòng chảy sản phẩm.
- Tăng Dung Lượng Bộ Đệm Trước Trạm Điểm Nghẽn Nếu một bộ đệm trước điểm nghẽn có xu hướng tích tụ lượng lớn WIP, tăng dung lượng của bộ đệm này giúp giảm áp lực cho máy phía sau và tránh tình trạng chặn.
Ví dụ thực tiễn: Trong ngành công nghiệp thực phẩm, nếu trạm đóng gói bị tắc nghẽn, tăng dung lượng bộ đệm trước trạm này có thể giúp quá trình đóng gói diễn ra trơn tru hơn.
- Tăng Hiệu Suất Hoặc Giảm Thời Gian Xử Lý Của Máy Điểm Nghẽn Để tối ưu hóa hệ thống, doanh nghiệp có thể tập trung vào nâng cao hiệu suất hoặc giảm thời gian xử lý của máy ở giai đoạn điểm nghẽn, giúp quy trình hoạt động mượt mà hơn.
Ví dụ thực tiễn: Trong dây chuyền sản xuất ô tô, cải tiến hiệu suất máy hàn giúp giảm thiểu thời gian chờ đợi và cải thiện năng suất tổng thể.
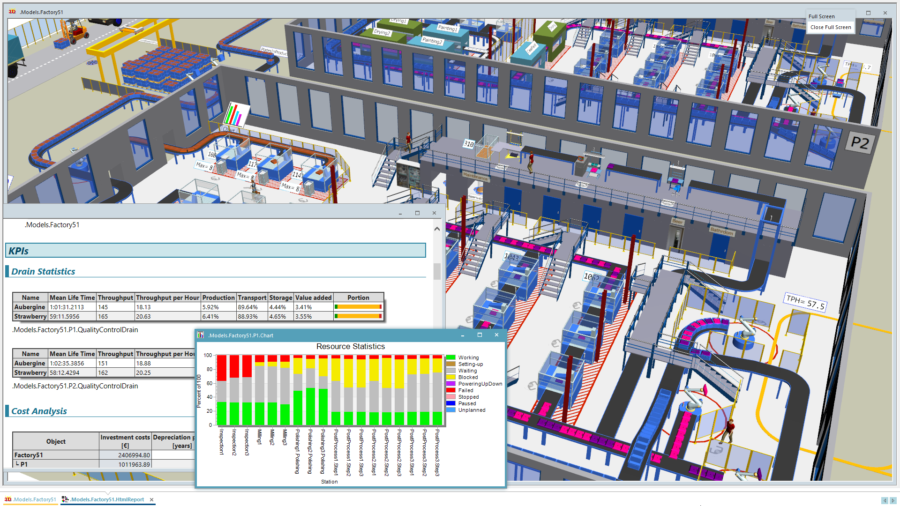
Suy Nghĩ Của Tôi
Là một chuyên gia tư vấn giải pháp Tecnomatix Plant Simulation, tôi nhận thấy rằng việc xác định và khắc phục điểm nghẽn là yếu tố quan trọng để đạt hiệu quả vận hành tối ưu trong sản xuất và logistics. Mỗi doanh nghiệp sẽ có cấu trúc hệ thống và các điểm nghẽn riêng biệt.
Plant Simulation không chỉ giúp nhận diện điểm nghẽn mà còn cho phép thử nghiệm nhiều giải pháp khác nhau, giúp doanh nghiệp đưa ra quyết định dựa trên dữ liệu thực tế. Sự linh hoạt và mạnh mẽ của công cụ này là lợi thế lớn, đặc biệt khi doanh nghiệp cần điều chỉnh nhanh chóng trước các yêu cầu thay đổi.
Liên hệ để biết thêm chi tiết và trải nghiệm Tecnomatix Plant Simulation
📞 Điện thoại: +84 976-099-099
📧 Email: lpthanh.plm@gmail.com
🌐 Website: https://phanthanh.id.vn | https://plm.id.vn
📌 Facebook: Lưu Phan Thanh – PLM Consultant
📌 LinkedIn: LinkedIn của Thanh
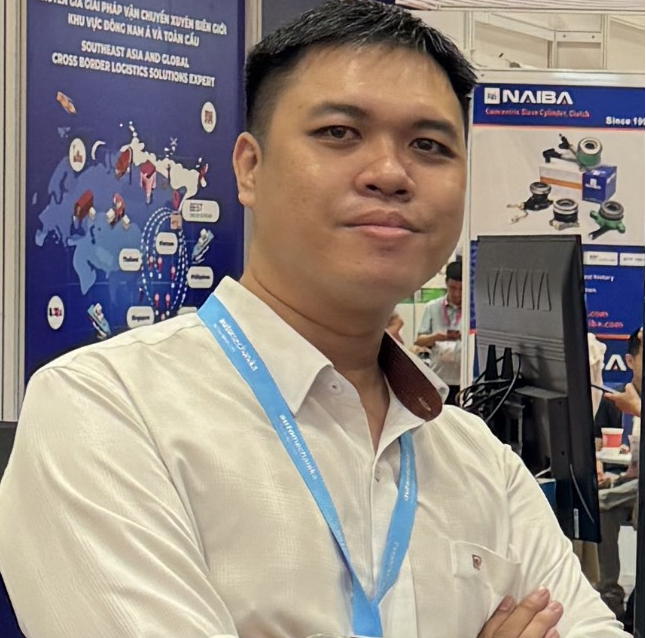
Experienced in Healthcare IT, I specialize in implementing and optimizing PACS, HIS/RIS, and HL7-FHIR interoperability to enhance efficiency and patient care. My expertise includes:
✔ PACS Solutions – Streamlining medical image storage, communication, and integration with HIS/RIS & HL7-FHIR systems – Ensuring seamless data exchange across healthcare systems.
Passionate about digital transformation in healthcare, I help organizations improve connectivity and operations. Let’s connect!
Luu Phan Thanh (Tyler) Solutions Consultant at PACS Ecosystem Mobile +84 976 099 099
Web www.plm.id.vn Email tyler.luu@plm.id.vn / lpthanh.plm@gmail.com